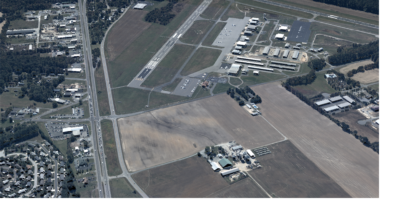
SPL100 Lidar data colored by RGB imagery from RCD30. Flown at nominal operational altitude, 12,500 ft, over Easton, Maryland with 50% line overlap.
In our July issue, managing editor Stewart Walker gave a lengthy account of the development and status of airborne lidar systems at the Leica Geosystems and Sigma Space subsidiaries of Hexagon. This was drawn mainly from an interview with Ron Roth, Product Manager—Airborne Topographic LiDAR for Hexagon’s Geospatial Content Solutions. The discussion touched on the addition of single-photon technology to Hexagon’s portfolio—and that’s where the article ended—but then Stewart spent time with founder and CEO of Sigma Space, Dr. Marcos Sirota, after which Ron hosted a tour of the assembly and test areas of the production facility in Lanham, Maryland. This is the sequel, therefore, and describes what Stewart discovered at Sigma Space.
Editor’s note: A PDF of this article as it appeared in the magazine is available HERE.
Single-photon: setting the scene
Sigma Space’s Single-Photon Lidar (SPL) technology has been well reported in these pages before, by Dr. Stephen Mitchell1, formerly director of mechanical engineering at Sigma Space and now with University of Maryland College Park (UMCP). At the time of my visit the ATLAS sensor for the NASA mission ICESat-2 had passed its tests at NASA Goddard Space Flight Center (GSFC) and was on its way to Gilbert, Arizona, for integration on to the spacecraft by its constructor, Orbital ATK (now Northrop Grumman). The launch took place on 15 September 2018 and LIDAR Magazine was in attendance!
Ron summarized the motivation for the acquisition of Sigma Space as the potential to accelerate the commercial applications of SPL technology. The ongoing business of Sigma Space was focused on clients such as DoD and NASA. Sigma Space had many successful single-photon instruments in operation and a proven capability to construct operational instruments at low production levels. Leica Geosystems saw this as an opportunity.
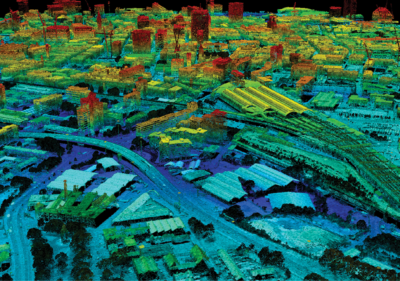
SPL100 data from the city of Manchester, United Kingdom, from two passes flown at 7500 ft and 140 knots. Courtesy of COWI A/S (Denmark).
The advance of linear-mode lidar is constrained in some ways by eye safety. Using two lasers is not a reasonable solution. It is not possible merely to fly at the same altitude and increase laser power to achieve higher pulse rates without suffering consequences in eye safety due to that increased output. If it is not possible to use more power, an alternative is to increase the size of the receiving optics, but this increases the size and weight of the airborne system. The better solution is to increase the sensitivity of the receiver, with the result that the pulse rate can be increased without requiring more power. This is where single-photon comes in—the receiver can detect as little as one arriving photon. The Leica TerrainMapper, for example, which is the latest model in the linear-mode lidar product range, uses a 20W laser to acquire 2 million points per second, i.e. 2 million effective laser shots per second (2 MHz). The ALS80 uses a similar 20W laser at 1 MHz effective pulse rate. The SPL100, however, obtains 6 MHz effective pulse rate from a 5W laser. The innovative underlying technology, through breaking up a single laser output into 100 beams, is capable of a pulse rate three times greater than that of TerrainMapper with one quarter of the laser power, i.e. is more than an order of magnitude more sensitive on the receiving end, giving extremely high effective pulse rates from a relatively small laser2. Leica Geosystems appreciated the market requirement and knew that Sigma Space had the know-how.
I asked Ron about the other exciting new lidar technology, Geiger-mode. He replied that, like single-photon, it uses a 2D array of detectors. However, unlike Geiger-mode, single-photon acts more like an array of linear-mode systems, making range measurements to intercepting surfaces at multiple ranges from a single output laser pulse, whereas Geiger-mode is limited to a single return per pixel per laser pulse. In order to overcome this limitation, Geiger systems work in a “photon starved” mode, with a very low probability of detection per pixel per pulse, and rely on dramatic repeat-sampling to separate signal from noise and improve accuracy. Leica Geosystems perceived that single-photon was a superior technology and pursued it. It recognized opportunities for using the technology in wide-area acquisition, for example for the HxGN Content Program.
I invited Ron to explain the implementation of single-photon technology in the SPL100 in more detail. One of the great advantages of SPL systems is a very short detection reset time, or minimum return separation in terms of vertical distance, which currently permits 24 cm range discrimination between separate targets. This is similar to that of the latest linear-mode systems, though better than the ALS80, for which the corresponding figure is >1 m. It is very suitable for acquiring the ground in low-brush—on a par with the full-waveform linear-mode systems. This makes single-photon technology very competitive. Ron repeated that Geiger-mode is limited by significant amounts of repeat looks at the same target and setting low detection probabilities of perhaps 35% or less. That means a probability of only 35% of detecting a returning photon: sensing all the vegetation as well as the ground is challenging without considerable repeat-sampling.
Ron enthused over single-photon being analogous to 100 linear-mode systems in parallel. I probed further by asking whether single-photon technology can provide intensity values. Ron explained that multiple photons from a single return produce a wider pulse at the detector. It is possible to time the leading and trailing edges of the incoming signals. Intensity is derived from the return pulse width and Sigma’s SPL timer is capable of resolving the leading and trailing edges of each return with 80 picoseconds (ps) resolution.
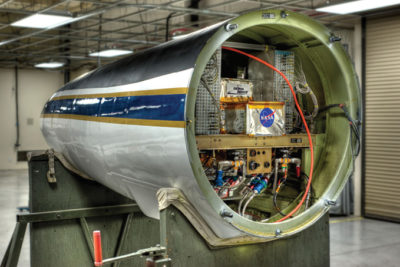
NASA Goddard’s Multiple Altimeter Beam Experimental Lidar (MABEL) mounted in nose cone of NASA’s ER-2 (shown right). Flew at 65,000 ft to validate algorithms for ICESat-2.
The wavelength of the laser in the SPL100 is 532 nanometers (nm), though others are possible. This is partly historical: earlier generations of photo-multiplier arrays, which were used in early products, had peak sensitivity in the visible. One advantage of 532 nm is water penetration, but as yet there are no algorithms in the SPL100 software to exploit this, e.g. water surface detection, refractive ray bending, speed of light change, so the system is not targeting bathymetric applications. Moreover, the SPL100’s canopy penetration is rather good. Some of the earliest single-photon systems were designed for that: it behaves like a multi-return linear-mode lidar for detection of forest floor. We moved on to geometric accuracy: delivered data, after calibration and registration, is stated to be in the 5-10 cm accuracy range in terms of RMSEZ. Leica Geosystems has made amazing progress in terms of achievable accuracies. The point density, usually measured in points per square meter (ppsm), is based on effective pulse rate, flying height, flight speed, wedge angle etc., allowing users the flexibility to tailor operating settings (within limits) to the point density requirements.
The SPL100 was not fully productized by Sigma Space at the time of acquisition. Thus re-engineering began immediately. Leica Geosystems approved the building of several units as part of productization. The sales network and content programs were activated in a “controlled rollout” mode for the SPL100, while experience was being gained. Existing Leica Geosystems components were integrated into the system, e.g. PAV100 gyro-stabilized mount, RCD30 medium-format frame camera, FlightPro software for mission execution, and MissionPro software for mission planning. Collectively, these Leica Geosystems components are known as the Common Sensor Platform, including pilot display, operator display, GNSS/IMU, data logging, and stabilized platform. The SPL100 is built in the Sigma Space facility in Lanham, whereas the Common Sensor Platform comes from Heerbrugg, Switzerland, where products such as the ALS80 and TerrainMapper are manufactured.
Leica Geosystems is transitioning the SPL100 into a fully commercialized system and is conducting pilot projects with partners, e.g., Woolpert in South Dakota early in 2018, and sample projects in Europe, e.g. the region of Navarro in northern Spain. Ron estimated that these systems are a minimum of 3x, but more likely 6-10x, as productive as linear-mode, which can achieve 2 MHz only up to certain flying heights. Woolpert, which has a long history of working with Leica Geosystems and Sigma Space, flew the SPL100 in Hawaii, where it performed well over lava fields with relatively low reflectivity.
As we neared the end of the session, I asked Ron to speculate on the value of single-photon technology for TLS or MMS systems. He felt there could be some. He said one company makes a single-photon lidar for UAVs—so small units for terrestrial use should be feasible. There’s no particular reason why the technology can’t be miniaturized.
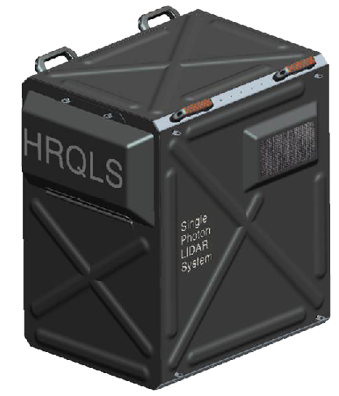
HRQLS (High Resolution Quantum Lidar System). Altitude: 6,000 to 10,000 ft AGL. Platforms: King Air 90 and B200.
The story of Sigma Space
I joined Marcos in his office to talk about Sigma Space and its history. The company was founded in 1997 to make optical instruments for aerospace. It began with the NASA ICESat mission, which carried a linear-mode waveform lidar. Born in Argentina, Marcos completed his PhD at the University of Washington in 1989, went to NASA as a post-doc, then worked at GSFC and University of Maryland Baltimore County. Sigma Space’s operations began in April 1998. His aspiration was not a classical service supplier but a company that created technology. He perceived a void amongst NASA suppliers for constructing and designing systems from proof of concept technical readiness level 6 (TRL6: a technology is usually tested in aircraft before it is used in space). His idea was an engineering development company working in cooperation with NASA. Sigma Space started to work on single-photon sensitive technologies early on, first on an airborne lidar for the measurement of cloud physical properties with Dr. Matthew McGill, and, soon after, on the commercialization of the Micropulse Lidar, a ground-based instrument to measure cloud and aerosols, developed by Dr. Jim Spinhirne. Dr. John Degnan, who became Sigma Space’s chief scientist in 2003, was at NASA at the time, and Sigma Space worked with him on the first single-channel and four-channel single-photon terrestrial altimeters. A patent was filed and a license exists today. GSFC launched the Mercury Laser Altimeter (MLA) in 2004. At the time the laser altimeters going to space were conventional, single-channel (i.e., just one beam), linear-mode lidars.
Sigma Space’s first success for their technology was a USAF Small Business Innovation Research award, for a 100-beam system (not unlike the SPL100) capable of operating at 3000′, which flew in 2006. Marcos had a very good electronics group, which designed the timers, truly the core of the instrument, and the result was a resounding success according to the Air Force Research Laboratory (AFRL) program manager, Richard Richmond. They found a plane nearby: UMCP had an aircraft with a hole for a sensor, since it had been testing instruments for USAF. Sigma Space flew and tested the instrument rather ahead of the schedule expected by the more formal AFRL. USAF, GSFC and UMCP were all very enthusiastic about the results. The system, known as Leafcutter, was later flown over both forest and ice, for example over Greenland, the data going to NASA. The University of Texas purchased a copy of the system for its Antarctic campaigns. After Leafcutter came Mini-ATM for NASA to monitor Greenland’s ice sheets, intended to fly in a UAV. There were also various scientific instruments, mainly for NASA, which were not lidar but contributed to the intense build-up of expertise in the company.

SPL100 mounted on PAV100 gyro-stabilized platform. Complete flight suite including RCD30 camera controller and FlightPro units shown.
A current version of the technology was selected for the instrument for ICESat-2—SPL is in space! The instrument is the Advanced Topographic Laser Altimeter (ATLAS), which has six beamlets. To create datasets similar to those to be measured in space, Sigma Space collaborated with NASA to build an instrument called Multiple Altimeter Beam Experimental Lidar (MABEL) for tests on the ER-2 aircraft at 65,000′, sufficiently high to have most of the atmosphere below the aircraft. The first of these flights was in 2010. MABEL was a GSFC project, but Sigma Space was very involved, providing electronics, mechanical assembly and more. A fundamental component of the instrument for ICESat-2 is the timing electronics, developed by Sigma Space. In addition Sigma Space provided the opto-mechanical components for, and built in-house, the laser pointing and boresight determination system, the ATLAS Laser Reference System. The principal investigator for the ER-2 mission was Dr. Matthew McGill. The project scientist for ICESat-2 is Dr. Thorsten Markus.
Marcos and I very briefly talked about automotive applications, but returned quickly to aerospace. Around 2011, Marcos decided to go for something more powerful than Leafcutter, upgraded for higher altitude, so Sigma Space built the HRQLS-1 (pronounced “hercules”), capable of operation at 7000′ with 50 cm pixels, giving a density of 8 ppsm in a single pass. This was used, for instance, for a Connecticut collect for USGS, flown in 2015. The purpose was the validation of the technology for the USGS 3DEP program.
Also, around 2011, Sigma Space worked with Woolpert to design and engineer a High Altitude Lidar (HAL) system for use at altitudes greater than 25,000’. Although Sigma Space SPL systems were operating at only 3,000’ when it initially become involved in HAL, the company saw that the high altitude system was feasible and signed up to build it. A requirement for this project was that the system had to be mountable in a wing pod, restricting form factor and mass. Ultimately, the system was tested and achieved initial operating capability (IOC) status after hundreds of hours of flight testing and the development of two prototypes. As a result, Sigma Space has built five instruments, three in the same configuration as the first, and two under Leica Geosystems, named the SPL100HA, which is similar to the commercial instrument, SPL100, but has a higher power laser so it works at higher altitudes. The two SPL100HA units were delivered in December 2017, capable of operating at 200 kts and up to 30,000′.
From HRQLS-1, Sigma Space advanced to HRQLS-2, still with 50 cm footprint spacing within the 10 x 10 array, but with a bigger laser to enable operation at 12,000′, which offered advantages in terms of air traffic control. As they were finishing HRQLS-2, a positive report was announced by USGS on HRQLS-1. Sigma Space participated in the ILMF conference for three years and Leica Geosystems became interested in the new technology. The HxGN Content Program was a major driver, too. Today, the SPL100 is offered to partners as a tool for content generation. The partners can perform as much of the workflow as they want, for example flying and processing, or just flying. Sometimes Leica Geosystems flies the instrument itself, using Northwest Geomatics’ aircraft, or a partner aircraft, or Dynamic Aviation, which also carries out many of the test flights of Sigma Space’s DoD instruments.
Sigma Space was seeking a large partner to put the technology to greater use. Sigma Space had also considered data services, so there was a meeting of the minds between the two companies. The deal became a full acquisition, however, to satisfy stakeholders such as the workforce, which was very necessary both on the commercial side and for NASA work—there was no obvious dismemberment to fit the bill. Sigma Space was acquired in early 2016 by Hexagon as a subsidiary of Leica Geosystems. Recently, operation of Sigma Space was transferred to Hexagon US Federal, the arm of Hexagon doing business with the federal government and DoD. There is already a long history and much experience of defense work at Hexagon Federal, starting from the federal systems arms of ERDAS and Intergraph. Nevertheless, Sigma Space will continue to produce instruments for Leica Geosystems and develop commercial technology jointly with Leica Geosystems. Marcos is very proud of what has been accomplished.
I raised the issue of intensity values, just as I had with Ron earlier in the day. Marcos explained that intensity, by definition, is the number of photons that return—what a linear-mode system records. Single-photon systems work with 100 beams that are like linear-mode but with fewer photons and much more sensitive detectors. Thus the returning signal does provide a measurement of intensity on a per pulse basis. By contrast, Geiger-mode has to do this by repeat-sampling: those systems have low probability of return. Only after the Geiger-mode system fires many shots at a particular point on the ground can it retrieve an “intensity” based on the number of returns versus number of pulses fired. But this is very processing-intensive. It is also very dependent on the GNSS/IMU accuracy.
I also asked about the bathymetric side and Marcos said there are export restrictions in play, depending on the capability of the system—bathymetric surveying has become very sensitive worldwide. Sigma Space has not developed any bathymetric capabilities or software. Bathymetry is also a difficult problem (what’s happening to 100 beams under the water, both on the surface and in the water column, plus the refraction issues), so Sigma Space will refrain from this market unless Hexagon uncovers some unexpected market requirements. Also, Sigma Space is moving to use 1064 nm, so water penetration will no longer be possible, though this change will help for generating breaklines at the land/water interface. There would be some advantages in an even more radical change, to 1550 nm, but Marcos argued that this is not so good for some applications. So 1064 nm is a comfortable choice on both physics and engineering grounds. I similarly repeated my question on TLS or MMS possibilities. Marcos said there are some reasons to develop SPL for such applications.
Does vertical accuracy remain the same as you fly higher? Marcos gave further explanation. Altitude does not affect timing accuracy. The accuracy of 3D points depends on the accuracy of both timing and geopositioning. As you fly higher, the vector is longer, so the results are directly affected by the performance of the GNSS/IMU system, but mainly in X and Y rather than Z. Timing is the biggest influence on Z. What influences timing? The length of the pulse of the laser is an important factor—the sharper the better—and is a function of the physics of the laser. There is jitter in the detector and jitter in timing. These factors are all the same at 25,000′ as at 3000′. Thus the error source that is worst affected by increasing altitude is geolocation.
Sigma Space SPL timer resolution is 80 ps, but 2 ps has been achieved for a NASA project. And the next generation timer is in the making. Hexagon has a European partner which has demonstrated the SPL100 to acquire data for infrastructure. Demonstrations are necessary because the process to start a national campaign is long and complex. The data can be used for construction and engineering work. In these applications, much higher spatial resolutions could be helpful given the level of detail that could be requested. The recognition of types of trees, as in a recent Minnesota collect, would benefit from higher resolution too. Thus, much higher data rates or “points per second” are in the plans. With the spread of GPUs, moreover, processing costs will fall considerably. Sigma Space is also moving towards real-time processing.
We spoke about ILMF and its power as a platform for the proselytization of new technologies, attracting the best speakers on the development side as well as the professional. Marcos concluded our enthralling discussion with the comment, “It [ILMF] has achieved a very high scientific content.” Yes, indeed.
On the shop floor
After lunch, Ron took me on a tour of the laboratory, where Bruce McCready showed me a system in the testing process. I noticed similarities to the ALS systems that I remembered from years ago, in terms of the rack arrangement and the complex wiring for power distribution, but of course the overall appearance was much more modern and sophisticated, including the Leica CC33 Camera Controller, GNSS/IMU and data logger. There is both flight planning and flight execution software. They still use a laptop to control the SPL100 sensor, because the sensor GUI is not integrated in the Leica FlightPro software, yet. Once it is incorporated, however, data will go straight to the Camera Controller, a useful simplification. Ron added that, while many ALS customers do not use a gyro-stabilized mount, all SPL100 customers do due to the higher flight altitudes.
A silver box on the sensor head contains the 5W laser, similar in physical size to the one used on the ALS80. While the standard SPL100 uses a 5-watt laser, the HAL and SPL100HA systems are designed for operation at greater flying heights and use a 15-watt laser. Ron pointed out that, while the lasers in linear-mode systems such as the ALS80 output laser pulses of 3 ns duration, SPL technology uses pulses as short as 100 ps. This simple comparison highlights the innovative nature of the Sigma Space technology.
End note
Ron returned to work and I spent the remainder of the day with Sigma Space scientist Claudia Carabajal, who works as a NASA contractor and has been heavily involved in ICESat, ICESat-2 and other missions. She took me on a memorable tour of GSFC, during which I saw instruments in testing as well as the workspace where the ATLAS instrument for ICESat-2 had successfully completed its tests before being shipped to Arizona. I met several brilliant NASA scientists, including Scott Luthcke, who gave a spectacular closing keynote at the ILMF conference in Denver in February—and will give a repeat performance, by popular request, at the January 2019 event. Claudia is writing an article on spaceborne lidar for LIDAR Magazine.
As noted in my editorial in this issue, I was privileged to attend HxGN LIVE in Las Vegas in June 2018. During the hectic four days, I was awarded a generous time-slot to talk to Bruce Wald about the HxGN Content Program. Bruce’s business expertise provided insightful perspectives and I hope that we can cooperate on an article on this topic, which will be the fourth and final one in this series.
The main purpose of the day, however, had been fulfilled. I had caught up with Ron Roth and seen the ongoing integration of Sigma Space into Hexagon. I had had the honor of more than an hour with Marcos Sirota and now understood some of the brilliance, motivation and sheer scientific and engineering excellence and innovation that undergird the achievements of Sigma Space and have rendered it so very attractive to its new owner. There is no question that the Sigma Space instruments, with their capability for higher altitudes, higher flying speeds and faster data acquisition, will enjoy a growing role, not only in terms of instruments sold to customers within Leica Geosystems’ traditional business model but also as resources for valued partners in the content program. Similarly, the company’s role in space and defense programs seems bound to expand—the future is as bright as it is intriguing.