SICK GmbH, founded by Dr. Erwin Sick in 1946, is a large European manufacturer of sensors and sensor solutions, offering a wide portfolio of more than 40,000 products aimed at an astonishing spectrum of industrial applications. It is perhaps less well known in the world of geospatial lidar than some others, so LIDAR Magazine seized avidly on an invitation to visit the company. In late 2018, publisher Allen Cheves and managing editor Stewart Walker toured the SICK plants in Reute and Waldkirch, Baden-Württemberg, Germany. Here is what they discovered.
The day of the visit
The drive to SICK in Reute (Figure 1) was a privilege in itself, through the spectacular southwest German countryside as it gloried in an Indian summer. We were hosted by Carolin Baumgartner, strategic product manager, 3D lidar sensors, and Harald Weber, head of product management, ranging. The plant consisted of a mixture of buildings of different ages and its pristine appearance struck us. The Reute campus hosts production of many components and sensors, including lidar R&D, product management, as well as product testing, where the elaborate facilities include a state-of-the-art rain chamber and many other testing facilities.
Editor’s note: A PDF of this article as it appeared in the magazine is available HERE.
Harald Weber is head of medium- and long-range lidar. He joined in 1996 in sales and started in 2D lidar for industrial applications. He anticipated much wider opportunities for the product range. Then he moved to product management. So he has had significant exposure to lidar over the years. He had been involved with robots playing games at university and this led to thoughts about an automated lawnmower. He was involved in projects with Carnegie Mellon University, which used SICK lidar units in its Groundhog autonomous vehicle (AV) in 2002. Now he’s been with SICK for 21 years, though such lengthy employment is unusual these days. SICK’s expertise is in sensors to steer processes as well as industrial automation, yet the company is increasingly involved in MMS and lidar from drones.
Carolin Baumgartner joined SICK in 2010. She has been leading product management for the LMS1xx family and in the last year has been instrumental in bringing to market the new 3D LiDAR family MRS1000 and as well as the 2D lidar LMS1000. During the last decade she worked with customers in all kinds of industries from agriculture to mining and automation, to enable the successful integration of lidar products in various applications. Currently her focus is to develop the 3D lidar portfolio of SICK for industrial applications. Carolin gave the company overview.
Background on SICK
The founder of the company, Dr. Erwin Sick (Figure 2), was a passionate inventor. Born in Heilbronn in 1909, he apprenticed in optics and worked in the laboratories of several leading companies. He married Gisela Neumann in 1944 and the following year started on his own, working from a former barracks in Vaterstetten, near Munich. Seeing other firms concentrating on optics or electronics, but not both, he single-mindedly followed his technological development aims to produce opto-electronic devices, supporting his family with earnings from selling radios that he made himself. He founded what was later to become SICK AG on 26 September 1946. He was apolitical, so received a permit from the American military government to practice his profession as an engineer. After a slow start, orders flowed from 1949 onwards.
In 1950, SICK introduced its first photoelectric switch based on an autocollimation principle. The following year, at the German Inventor and New Development Trade Fair in Munich, Sick presented the first wooden model of his “light curtain” and received a certificate for exceptional creative performance. This invention, based on the same autocollimation principle was the technical breakthrough that would form the basis of an entire range of devices. The first marketable accident prevention light curtain (Figure 3) debuted in 1952 at the Second International Machine Tool Trade Fair in Hanover. The orders that followed led to serial production and eventually to the company’s economic breakthrough.
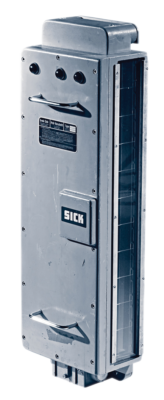
Above: SICK ANM006 LVU—one of the first sensors based on the light curtain principle to enter large-scale production.
The location decision to Waldkirch was an interesting one. In 1954, Sick tried in vain to obtain a loan from the Free State of Bavaria to build up the company. When Baden-Württemberg offered to lend him the money he needed, he moved from Munich to Oberkirch in Baden and, in 1956, the company and its 25 employees were relocated to Waldkirch. In October that year, he was granted the patent for a new type of photoelectric retro-reflective sensor that would later become the product with one of the company’s strongest sales performances. Twenty-one years later, the company moved into its new premises on Sebastian-Kneipp-Strasse, which remains the company’s headquarters to this day. As it grew, Sick received a series of awards. Erwin Sick died in 1988 at age 79. His widow, Gisela (Figure 4), has continued to be involved with the company and has initiated several community projects including kindergarten education and music projects at the edge of the campus.
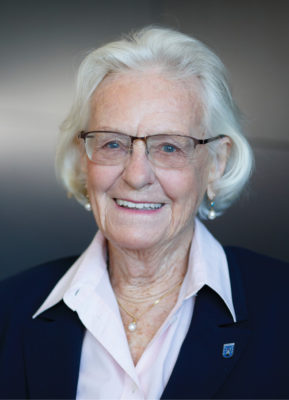
Figure 4: Frau Gisela Sick, who has been involved with the company since its foundation and remains involved in community initiatives on the firm’s campuses.
Carolin pointed us to several videos the company has posted on YouTube. SICK presents itself as, “worldwide, one of the leading manufacturers of sensors and sensor solutions for industrial applications”. She emphasized the autocollimation technology and the light curtain, which stopped a machine when someone reached in. As word spread, SICK made more and more of them. 1972 saw the start of internationalization, with a presence in France. In 2013 it exceeded €1b in revenue. Besides production in Waldkirch, Reute and other locations in Germany, manufacturing takes place in Minneapolis, MN; Hungary; China; and Malaysia. There are also three Regional Competence Centres—the German one has been copied in Asia and US—and six development centers in addition to the one at headquarters. The distribution model is a familiar one: much of the world is covered by subsidiaries and representatives, but third-party “agencies” do the work in some countries. The 2017 numbers were: orders €1.543b, sales €1.512b, EBIT €149m, R&D expenditure €169m—more than 10% of sales is spent on R&D. The number of employees is growing at 10% per annum: there were 8809 in 2017, of whom 5224 were in Germany and more than 900 were engineers, compared to 1700 in 1996. Carolin stressed the importance of a flow of young employees to maintain the company’s technical strength: in 2017 there were 324 trainees. The company has dual arrangements with colleges. There are five men on the Executive Board, chaired by Dr. Robert Bauer, but there have also been women over the years!
Carolin emphasized the continuity and showed an impressive time series of developments. SICK sensors are focused on the automation of three areas: factory, logistics and process automation. The second and third of these include numerous applications of distance measurements using lidar; these are not expressly geospatial and the majority are short-range in terms of requirements. In 2016 the SICK AppSpace concept was introduced, which the company describes as, “… intelligent software tools, high-performance programmable devices, and a dynamic developer community create a solid foundation for designing customized sensor solutions”, i.e. it provides capabilities to create and manage bespoke application solutions. SICK’s emphasis on quality—the toughness of its products to perform for many years in tough industrial environments—was a theme stressed throughout our visit. There is also an increasing emphasis on services. In terms of company structure, SICK divides its activities into nine broad product generating divisions known as Global Business Centers: Carolin and Harry are in identification and measuring.
Lidar at SICK
There are 15 2D and 3D lidar sensor families in the SICK portfolio. Their history stretches back to 1968, when the company launched Watchman, the forefather of the PLS safety laser. In 1976, polygonal mirrors and laser diodes were introduced and in 1981, the first industrial use of the pulse-delay or time-of-flight method for distance measuring sensor technology. In 1989, SICK accomplished its first distance determination with laser light using this approach, operating at 20-25 Hz and giving a precision of 5 cm. Indeed, in 1991, this same principle was applied to the positioning of autonomous vehicles and was used in its first safety laser scanner two years later. In 1996, came the LMS200, the first of a series of laser scanners using the pulse-delay method for general indoor and outdoor industrial applications, with an accuracy down to 2 cm. SICK acquired a 90% stake in ibeo automotive in Hamburg in 2000. Ibeo also developed a sensor for Trimble, which to this day is in SICK’s on-site museum in Waldkirch.
In the first DARPA Grand Challenge in 2004, not only the CarnegicMellon Sandstorm but several other contestants sported SICK lidars. They were popular in 2005 too: Carnegie Mellon entered an upgraded Sandstorm as well as H1ghlander, both of which carried four SICK lidars. Other teams embraced these sensors equally enthusiastically, including the winner, Stanley, a Lexus SUV from the Stanford SAIL lab led by guru Sebastian Thrun, who had moved there from Carnegic Mellon. The next event in the series was the DARPA Urban Challenge in 2007, in which both winner and runner-up carried SICK and ibeo lidars. The DARPA events fomented intense lidar development from SICK and its competitors, benefiting non-military applications too, such as earth-moving equipment, lawnmowers and UAVs. The SICK LD-MRS, at 0.77 kg with an IP69K (Ingress Protection) certification, has performed well on UAVs and the company’s lidars are offered, for example, on the mdLiDAR1000 system from Microdrones.
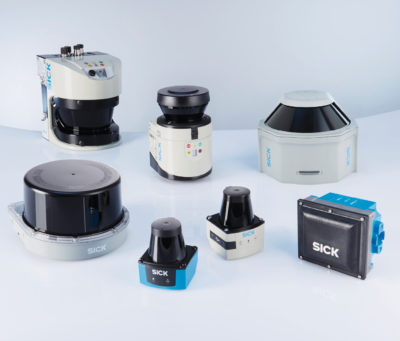
Figure 5: A sample from SICK’s current range of lidar sensors. Clockwise from top left: LMS5xx, LMS1xx, MRS6000, RMS320, TiM5xx, TiM1xx, MRS1000.
It took only 10 years to progress from the PLS to S3000, the current model of the safety laser. The LMS200, with a range of 30 m for black targets, was designed for and used heavily in outdoor industrial applications such as ports, toll collection systems and outdoor autonomous ground vehicles. Although phased out some years ago, many LMS200 systems are still in use owing to their impressive robustness. SICK first exploited multiple-echo technology in 2008 in the LMS1xx series (dual-echo-technology). The LMS500 (2010) is a multipurpose lidar, designed for outdoor applications, with 5 echoes and longer range (40-50 m to black targets, up to 120 m to more reflective ones). On the 2D side, the LMS1000, for example, uses a wavelength of 850 nm and scans, at a frequency of 150 Hz, over a field of 275° at 0.75° resolution, with three returns (multi-echo-technology). The maximum range is 64 m, but the unit is typically used in shorter-range applications and offers 16 m range to targets with 10% reflectivity and 30 m to 90%. The 2D sensors scan in a 2D plane, based on a rotating mirror or prism. The LMS is one of several product families—others are TiM, NAV and LD-LRS.
Whereas SICK’s 2D lidar systems scan in a single plane, the 3D ones build points clouds by scanning in more than one plane. There are numerous models in each category, some of which are shown in Figure 5). They use silicon laser sources with wavelengths in the 850-905 nm range. The company’s vibrant R&D activities ensure that the stream of developments will continue.
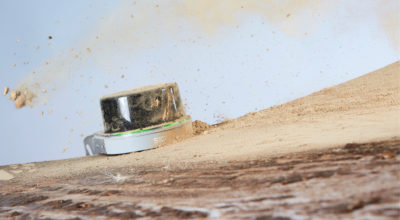
Figure 6: SICK MRS1000 3D laser scanner working in tough conditions—“outdoors is SICK’s fourth dimension”.
The 3D lidar sensors come in fewer families, so are a little easier to assimilate! These include the MRS1000 (Figure 6), giving 3D with measurement in four planes. This enables the sensor to view the ground and still see hanging objects in the direction of travel. Similar to the LMS1000, the MRS1000 has a wavelength of 850 nm and scans, at a frequency of 50 Hz, over a field of 275° horizontally and, through the four planes, 7.5° vertically, at an angular resolution of 0.25°, with three returns. The maximum range is 64 m, but the unit is typically used in shorter-range applications and offers 16 m range to targets with 10% reflectivity and 30 m to 90%. This sensor is especially designed for challenging outdoor applications such as collision prevention and driver assistance for all sorts of vehicles in applications such as factories, ports and mines, but also for reliable monitoring in traffic management, building security, access control and people counting. Navigation, both indoor and outdoor, e.g. in warehouses or agricultural environments, is another application focus. The latest model is the MRS6000, also designed for outdoor applications, with 24 planes. The corresponding figures for this sensor are: 850 nm; frequency of 10 Hz, over a field of 120° horizontally and, through the 24 planes, 15° vertically, at an angular resolution of 0.13° horizontally and 0.625° vertically, with four returns. The maximum range is 200 m, with 30 m range to targets with 10% reflectivity and 75 m to 90%. The third 3D lidar sensor is the especially rugged LD-MRS with four planes and working range up to 300 m.
The newest generation of lidar sensors uses SICK’s innovative, patented technologies HDDM and HDDM+. There are ~100 short laser pulses per measurement. They input multiple low-energy pulses to a statistical analysis to give the results1. To the author, there was a similarity in the thinking to that behind Geiger-mode lidar, though the underlying technology is not the same. The MRS1000, for example, uses HDDM+.
SICK also makes two radar sensors. The company emphasizes its “sensor intelligence” and use of all physical principles. The radar sensors are the RAS4xx and RMS3xx, aimed at collision avoidance and driver assistance, i.e. automotive applications in poor weather. The radar frequency is 24-24.5 GHz, corresponding to wavelengths of 12.5-12.2 mm.
SICK views the world as semi-automated, automated and autonomous. We discussed sensor complementarity, which of course is well known to SICK, with its portfolio of thousands of products. SICK and its customers have exceeded 54 billion hours of laser sensing. A gallimaufry of applications includes automated machines to position cars in a parking garage; measurement of bulk materials; movement of cranes, e.g. in ports; perimeter protection; stopping vehicles with overheated components from going into tunnels (with a combination of thermal camera and lidar sensor). The sensors have 10-15 years industrial life; as an additional service, SICK offers an extended warranty of up to 5 years which customers can book with their order. The company is driven by reliability and uses the catchphrase, “Outdoors is our fourth dimension.” Harsh environments are welcome, for example the LD-MRS has IP69K certification—it can withstand a high-pressure cleaner. Ports are salty and tunnels suffer from H2SO4—sulfuric acid—but SICK sensors sustain this challenge too. The conversation strayed on to start-ups that focus on automation on public roads; SICK does not have this aspiration, so does not perceive start-ups as a threat.
After the introduction, we enjoyed a factory tour, starting with the product test area. We saw sensors, for use in an airport, which monitor where the pieces of luggage are going. Testing is critical to SICK’s culture and success: the company accepts enormous expenses for testing. There is little compromise: all sensors, not a sample, undergo a variety of tests in special environments such as chambers, ovens and test ranges with targets. We saw testing of the LMS400, which FedEx and DHL use in a 3D grid to estimate volumes and weights of packages. SICK has full traceability of sensor parts. Continuous improvement is practiced assiduously. There are electronics to protect against oversaturation. The comprehensive nature of the test procedures, the set-up of the test environments and the commitment of the test workforce to excellence will not be easily forgotten!
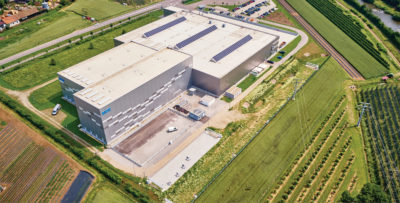
Figure 7: The SICK Outdoor Test Center in Waldkirch. In the foreground, the autonomous van can be seen on its test track, alongside several product test ranges. At the top right is the River Elz, which gives rise to the foggy conditions that facilitate the outdoor testing of lidar sensors.
Space is proving a problem as SICK has been growing with dramatic speed. The success stems from making “industrial sensors”, not just measurement devices. We drove to the plant in Waldkirch (Figure 7), where the customer center, distribution center and outdoor test center are housed. The campus experiences fog owing to a stream beside the factory, which facilitates the testing of sensors in demanding conditions. We were shown an electric autonomous vehicle, which is based on the vans used by the German post office. But our hosts stressed, very strongly indeed, that the van enables them to work with and demonstrate their sensors—it does not indicate that SICK has AV ambitions! The van was stacked with sensors of all kinds and in the back there were racks of electronics, including a SIM4000 (Sensor Integration Machine) controller and two large battery enclosures. The sensors have firmware that can be updated. We saw the van moving autonomously in a pre-programmed way by orientation on way points. SIM is part of the SICK AppSpace ecosystem and opens up new possibilities for application solutions. Data from SICK sensors and cameras can be merged into a point cloud, evaluated, archived, and transmitted, e.g. to cloud platforms, surely an indication of SICK’s ambitions beyond just sensors.
As SICK is dedicated to be one of the leading global manufacturers of sensors and sensor solutions, its wide variety of sensors, worldwide sales and service network, and customer-oriented developments are crucial success factors. With this worldwide network it is possible to support all kinds of different customers, such as port operators in Dubai or Singapore, mining companies in Australia or South Africa, or robotic manufacturers in the US or China. SICK customers can count on an outstanding level of application knowledge through the long-term experience and close customer relationship of the company’s international and national application engineers, product managers and industry managers.
We talked briefly about safety lidar sensors, which are in another portfolio, mainly indoors. Even 1.8% reflectivity still gets a signal. The lineage of these sensors can be traced all the way back to the light curtain.
Endnote
To those of us in geospatial lidar, especially on the airborne side, SICK has been rather a silent partner. Our visit, however, left a lasting impression, of a company rooted in the provision of sensors and other tools for use in industrial environments, ensuring through remarkably rigorous testing that the highest standards of ruggedness, quality and endurance would be met. The company supports a vibrant R&D activity for the development of new sensors and incremental improvements to existing ones. SICK is already a player in TLS, MMS and other aspects of geospatial lidar applications, and its role can only grow. We look forward to learning more about this successful enterprise, expanding from a family business to a multinational in seven decades, and we are already planning a second article, focused on a SICK customer.