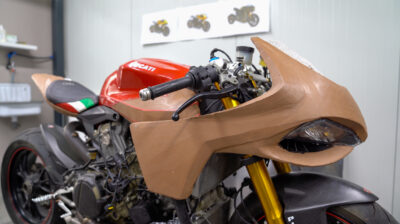
New designs for front apron and rear are shaped out of clay. Because the dry clay is shiny, it must be matted in order to be digitally captured. Photo: AESUB
Customised design for Ducati front apron and rear
Giving motorbikes an individual touch – that is what Luuc Muis has made his goal. The owner of LM Creations designs precisely-fitting components according to the customer’s requirements. He combines design, technology and craftsmanship in new vehicle parts. With technical know-how and skilled workmanship, he shapes new models out of clay. Luuc Muis makes models of prototypes; in some cases these are unique items.
Still no substitute for handcraft
Even if digitization is becoming more and more important, the handcrafting of items still has an important part to play when developing designs. Physical models provide a significantly better impression of the shape and design than digital ones. Fine details such as exposed edges can be easily overlooked in a digital CAD environment. With 1:1 models, fine-tuning can take place from a variety of perspectives.
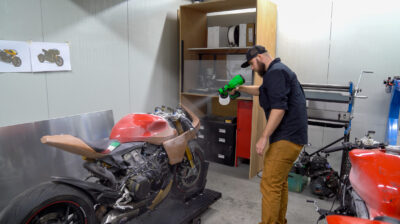
The scanning spray AESUB green is applied using a spray gun to the surfaces to be scanned. A homogeneous layer is generated within just a few seconds. Photo: AESUB
Individual touch for the Ducati Panigale
Luuc Muis redesigned the front apron and rear for a Ducati Panigale 1199 s in order to make the machine faster and more stylish. He shaped the desired design out of the initially pliable clay. The proportions and curves of the 1:1 model can be examined directly on the Ducati.
Matting the surfaces
Once the customer had approved the design, the model entered the digital world by means of hand-held scanners. The challenge here was that dried clay is shiny, which means the scanner light is reflected. As a result of these reflections, the dimensions of the parts cannot be captured precisely. For this reason, Luuc Muis matted the clay prior to the scan using a scanning spray. The process lasted just a few seconds, but saves lots of time during scanning and post-processing the scan data.
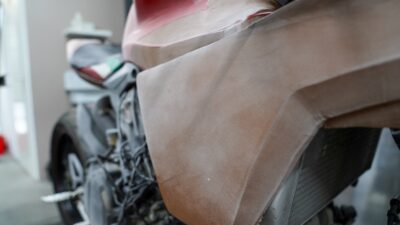
Thanks to the thin, white layer, high contrast values are produced on the part’s surface, which can then be easily captured by the scanner. The layer thicknesses are between 1µ and 15µm. Photo: AESUB
Even spray layer – no pigments
Having tried out several different sprays, Luuc Muis is now convinced by the AESUB scanning sprays. The reason: AESUB sprays are easy to handle, form a uniform layer, sublimate completely and are free from harmful pigments. “I spray the product onto the relevant part sections from a few centimetres away – and I can already scan what were previously shiny, reflective surfaces without a problem”, explains Luuc Muis. “It also works where there are deep grooves and recesses”, he continues. The applied spray dries very quickly and forms a fine, homogeneous layer. The layer is touch-dry, which means the part can be touched and e.g. positioned elsewhere. Reference points can be placed directly on the sprayed layer. “Another major advantage of the spray”, adds Luuc Muis, “is that the spray evaporates automatically and I do not have to clean the parts. This saves me a great deal of time, and makes the entire scanning process a lot more efficient and more comfortable.”
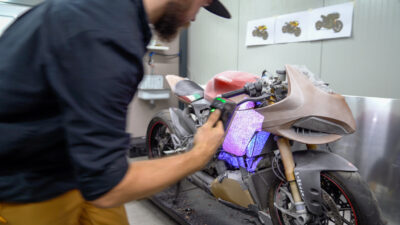
The matted parts are scanned. Through the spray, high contrast values have been generated, which means the scanner can capture the parts well. The spray sublimates after approx. six seconds. The sprayed parts do not need to be cleaned. Photo: AESUB
AESUB scanning sprays – different sublimation times and layer thicknesses
The AESUB scanning sprays are available with different sublimation times. Luuc Muis selects the particular spray variant according to the relevant application. If smaller parts require scanning, then AESUB blue is used. For large-scale parts he uses AESUB green, because it can be applied with a spray gun. For the front apron and rear of the Ducati he also used AESUB green.
Layer thicknesses between 1µ and 15µm
Spraying the surfaces takes just a few seconds. The thin, white layer gives rise to high contrast values on the parts’ surfaces, which can be easily captured by the scanner. The layer thicknesses range from 1µ to 15µm. The matting layer is touch-dry, so the parts can also be touched and repositioned during the scanning process. Reference points can be placed directly on the layer. They last significantly better than with conventional sprays.
Conventional scanning sprays: preparation and post-processing costs a lot of time
Compared with AESUB, the disadvantage of conventional sprays is that the parts and environment have to be cleaned thoroughly after measurement is completed. The spray layers are not as fine or uniform, which can impair the measurements results. The pigments present in many conventional sprays not only pose a risk to health but can also damage the sensitive measuring equipment. The health reasons are also a key factor for many users. Since many conventional sprays contain titanium dioxide, which is harmful to health, AESUB is increasingly the winner.
About AESUB
Scanningspray Vertriebs GmbH, Dortmund, founded in 2018, specialises in the development and manufacture of scanning sprays. With an in-depth knowledge of 3D scanning and aerosol generation, the AESUB products are being continuously developed so as to enable faster, more efficient, and more precise 3D scanning processes. www.aesub.com